Gute Chemie ist bei der E-Auto-Batterie nicht alles - man muss sie auch clever verstauen. Denn je mehr der Energie speichernden Aktivmaterialien, also chemisch aktive Komponenten, man ins Auto bekommt, desto grösser wird die Reichweite. Die Industrie wechselt daher zunehmend von der klassischen Modulbauweise zu einer kompakteren Variante. Die echte Revolution steht aber möglicherweise erst noch bevor.
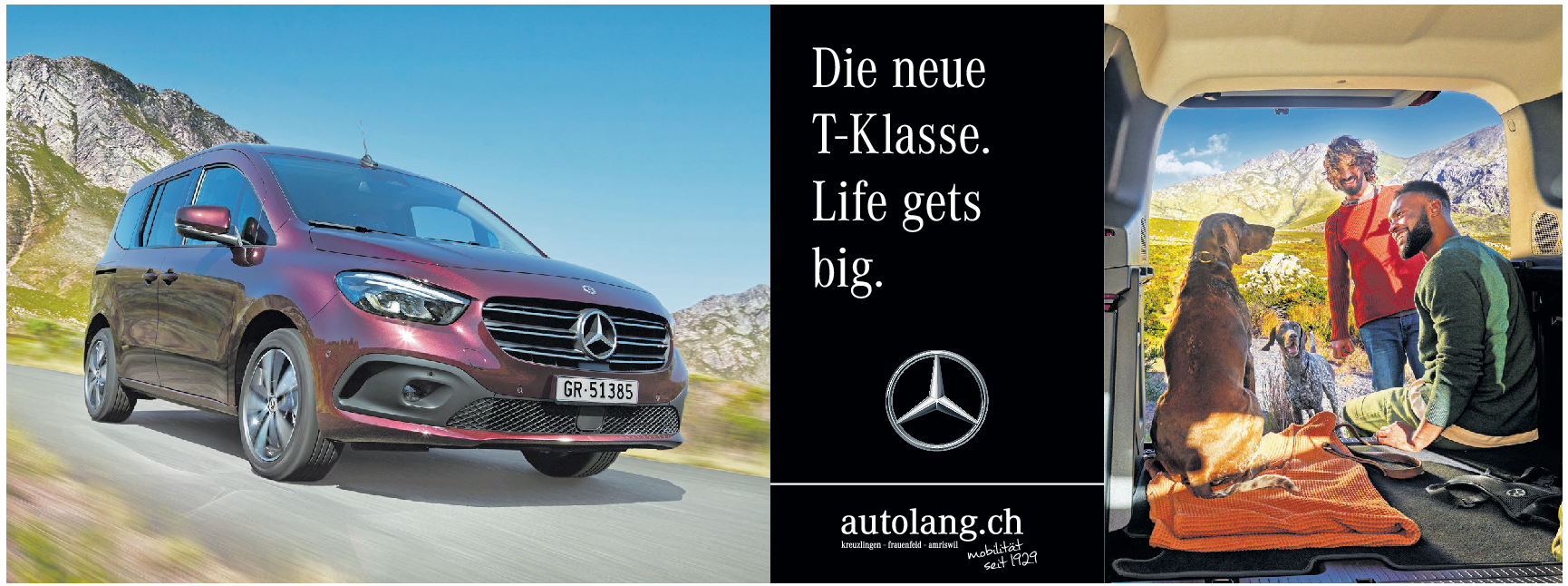
Grundbestandteil einer E-AutoTraktionsbatterie sind die einzelnen Batteriezellen. Traditionell werden sie beispielsweise im Dutzend zu sogenannten Modulen zusammengefasst, verbunden und in ein mehr oder weniger sperriges Gehäuse gesteckt. Diese leicht zu transportierenden und gut handhabbaren Module wiederum bilden zusammen die Batterie. VW montiert sieben bis zwölf davon zusammen, verbindet sie und steckt sie dann in ein weiteres, grösseres Gehäuse. Am Ende landet die Ausgangszelle also doppelt verpackt und mehrfach verkabelt im Auto. Besonders effizient ist das nicht.
Reparaturen sind bei Modulbauweise einfacher
Als erster Batteriehersteller hat das chinesische Unternehmen Catl daher 2019 diese redundante Bauweise aufgebrochen. Die sogenannte Cell-toPack-Technik überspringt die ansonsten übliche Modulebene kurzerhand und setzt das fertige Batteriepaket direkt aus den einzelnen Zellen zusammen. Verbindungselemente, mechanische Komponenten und Kunststoffteile können so eingespart werden. Wo dadurch Raum frei wird, ist Platz für mehr Aktivmaterialien - und somit auch mehr Speicherplatz für Energie. Die Kapazität bei gleichbleibendem Volumen steigt. Und damit die Reichweite des kompletten E-Autos.
Nur 50 Prozent Aktivmaterialien enthält ein durchschnittliches Batteriepaket für E-Autos. Für jedes Gramm, das Anode, Kathode und Elektrolyt auf die Waage bringen, kommt ein Gramm an Klebstoff, Schrauben und Verpackung dazu. Cell-to-Pack-Technik verbessert das Verhältnis deutlich. Allerdings auf Kosten der Reparierbarkeit. Bei einer Modulbatterie lassen sich schadhafte Module zumindest theoretisch herausnehmen und tauschen. Cell-to-Pack-Akkus hingegen muss man im Ganzen wechseln, wenn sie kaputt gehen. Das ist neben der simpleren Logistik und der einfachen Handhabung der wichtigste Grund, warum die PW-Industrie so lange an der Modulbauweise festgehalten hat.
Doch zuletzt gab es einen Strategiewandel. Auch, weil der Modultausch bei Kundenfahrzeugen in der Praxis kaum eine Rolle spielt - sei es aus praktischen Gründen oder wegen des schlechten Kosten-Nutzen-Verhältnisses. Stattdessen werden Gewicht, Volumen und Energiedichte bei der Batterie immer wichtiger.
Neben Tesla und dem chinesischen E-Auto-Giganten BYD hat auch VW angekündigt, künftig Cell-to-Pack-Batterien einsetzen zu wollen. Die neue Technik wird wohl Mitte des Jahrzehnts in der neuen E-Architektur des Konzerns zum Einsatz kommen, die im Rahmen des Projekts Artemis entwickelt wird. Sie soll unter anderem Luxusfahrzeuge von Audi und Bentley tragen.
Auf lange Sicht könnte Cell-to-Pack aber nur ein Zwischenschritt sein. Denn anstatt die Zellen erst in ein Batteriegehäuse und dann das ganze Paket ins Auto zu packen, könnte man sie auch gleich direkt in der Fahrzeugkarosserie unterbringen.
Cell-to-Chassis heisst dieser Ansatz, der bislang in der Serienproduktion aber noch nicht genutzt wird. Auf diesem Weg liesse sich die Kapazität von Batterien bei vergleichbarem Gewicht und Bauraumbedarf um rund ein Viertel gegenüber der Modulbauweise steigern. Berücksichtigt man auch kommende Verbesserungen bei der Zellchemie, könnten Reichweiten von 700 Kilometern künftig Standard werden. Heute sind es 300 bis 400 Kilometer.
Allerdings hat auch die Cell-to-Chassis-Technik nicht nur Vorteile. Denn ist die Reparierbarkeit schon bei Cell-to-Pack beschränkt, ist sie bei der direkten Integration in die Fahrzeugstruktur kaum mehr vorhanden.
Die Gleichteilestrategie stösst an ihre Grenzen
Auch bei Recycling und Unfallsicherheit sind noch Probleme zu lösen. So stellt sich etwa ganz praktisch die Frage, wo die Feuerwehr die Blechschere ansetzen kann, um ein Unfallopfer aus dem Fahrzeug zu befreien, wenn in jeder Karosseriestrebe Hochspannung stecken kann.
Soll der Bauraum möglichst effizient ausgenutzt werden, steigt zudem der Entwicklungsaufwand für Fahrzeugplattformen. Gleichzeitig gerät die Gleichteilestrategie an ihre Grenzen. Basieren heute etwa Autos unterschiedlicher Karosserieformen auf der gleichen Architektur, wäre das dann nicht mehr ohne weiteres möglich. Auch ein Batterie-Wechselsystem, wie es zurzeit der chinesische Autohersteller Nio in Europa etablieren will, funktioniert mit den hochintegrierten Zellen nicht.
Nicht nur deshalb ist fraglich, ob Cell-to-Chassis-Batterien eine Option für Massen-PW sind. Kosten und Aufwand könnten sie auf Sportwagen oder Luxusautos für die Langstrecke beschränken. Oder etwa für Fluggeräte interessant machen. Normale Autos würden im Alltag auch mit normierten Einheits-Packs zurechtkommen, wenn die Reichweite über die Zellchemie steigt und die Lücken in der Ladeinfrastruktur geschlossen werden. Holger Holzer
Ladeinfrastruktur in der EU
Zwischen dem EU-Land mit den meisten und dem mit den wenigsten Ladepunkten pro 100 Kilometer Strassenlänge liegen Welten. Nach Auswertung des europäischen Branchenverbands Acea sind in den Niederlanden 64,3, in Litauen nur 0,2 Ladepunkte vorhanden. Insgesamt gibt es in fünf Ländern rechnerisch keinen einzigen Ladepunkt pro 100 Kilometer Strassenlänge. 17 Länder verfügen über weniger als fünf Ladepunkte, nur fünf Länder weisen mehr als zehn Ladepunkte an dieser Streckenlänge auf. Zu den Top-5 zählen neben den Niederlanden noch Luxemburg (57,9), Deutschland (25,8), Portugal (24,9) und Schweden (12,2). Unter dem Begriff «Strasse» hat Acea Autobahnen, Schnell- und Landstrassen zusammengefasst. Wie gross die Unterschiede innerhalb Europas ausfallen, macht Acea mit dem Vergleich deutlich. So gibt es in den Niederlanden einen Ladepunkt pro 1,5 Kilometer Strassenlänge, im achtmal so grossen Polen ist statistisch gesehen ein Ladepunkt nur alle 150 Kilometer nutzbar. (spx)